摘要:分析了燒結機頭粉塵的特性,通過對機頭除塵器合理有效地改造,綜合利用特氟龍高性能涂料芒刺、聲波清灰等技術、措施,達到了控制粉塵排放濃度和減少粉塵排放總量的目的。 前言 在燒結生產操作過程中,產生大量含塵和含有SO2、NOX、PCDD/FS(二惡英)等有害氣體的煙氣。為保護環境、保護主抽風機轉子、提高燒結機的作業率,含塵煙氣在排至大氣前必須經機頭除塵設施凈化。隨著國家循環經濟、節能減排工作發展的要求,對粉塵的排放標準要求越來越高,2008年山東省修訂了《鋼鐵工業污染物地方排放標準》,燒結機頭煙氣粉塵排放濃度降低到90mg/m³。萊鋼燒結廠燒結機頭的粉塵排放濃度高達300~800mg/m³,燒結機頭煙氣治理被公司列為重點環保改造項目,2007年投入1300多萬元對燒結機頭煙塵排放進行系統治理。 11#、2#105㎡燒結機頭電除塵器提效改造的技術研究 1.11#、2#105㎡燒結機頭除塵器概況 萊鋼燒結廠目前擁有3臺105㎡燒結機,其中1#、2#105㎡燒結機分別配套125㎡臥式單室三電場電除塵器,分別于1993年6月、1995年5月投入使用,125㎡電除塵器技術參數見表1.燒結機經過擴容改造面積為132㎡,而除塵器及主抽風機均未做相應改造,所以粉塵排放嚴重超標。除塵器存在的問題主要有: (1)根據監測結果,煙塵排放濃度300~800mg/m³,嚴重超標。 (2)電除塵器電場作功效率低。電場電壓在20~40kv(額定72kv),電流在100~300mA,(額定1200mA),有時在100mA以下,甚至為零,除塵器做功效率不足20%。 (3)電除塵器內部極板掛灰較厚,電場頂部掛灰最為嚴重,以下次之;極板有變形現象;芒刺線尖端結球嚴重,陰極框架部分變形。 (4)灰倉倉壁粘灰、結塊、棚灰,堵塞下灰口,下灰不暢。 (5)極板極線均有不同程度的腐蝕現象,板、線下部腐蝕嚴重,以上次之。 1.2燒結煙氣的特性分析 機頭除塵器屬于工藝除塵,其性能在很大程度上受燒結生產煙氣的波動影響。燒結煙氣的特性主要有以下幾點: (1)煙氣溫度波動幅度大,變化區間為80℃~150℃。 (2)煙塵的比電阻值變化較大,為3.2*109~1.0*1012Ω.cm,屬于中、高比電阻值范圍。 (3)煙氣的含水量大,平均值為10.05%。 (4)煙塵中韓Na、K的氧化物和氯化物比較多,煙塵細而輕飄,灰塵呈絮狀,收塵難度加大,當煙氣流速大于 0.8~1m/s時,很容易被氣流帶走排至空中。 (5)煉鋼除塵灰、污泥、煉鐵除塵灰等多種固體廢棄均返回到燒結配料,造成煙氣中粉塵物化性質發生變化,其中的堿性物質提高粉塵的比電阻,不利于靜電收塵。 1.3影響除塵器除塵性能的原因分析 (1)除塵器能力不足,單位電除塵器面積(單位電除塵器面積系電除塵器面積與燒結機面積之比值)僅為0.95,遠遠落后于目前國內機頭除塵器的主流配置。 (2)兩臺125㎡電除塵器,投產于1993年和1995年,運行至今,設備嚴重老化,雖先后采取人孔門、灰斗等漏風點焊補、采用高性能密封墊等措施,防止漏風、結露,但漏風率很難保證設計值(<3%)多處漏風導致除塵器內部氣流湍流,除塵性能下降。 (3)極板、極線腐蝕率、變形率達到40%以上,由于漏風,當煙氣溫度低于漏點時,煙氣中所含的二氧化硫與冷凝水結合,形成酸性物質,導致極板、極線下部腐蝕嚴重;極板、極線強度降低、變形,極間距無法保證在450mm,導致電場強度分布不均勻,陽極板的利用率下降,除塵器除塵效率下降。 (4)三個電場全部為單側側旋轉錘振打,振打系統剛度不夠,振打力不足,電場頂部掛灰最為嚴重,以下次之,這種情況導致電流降低,二次電壓降低,除塵效率急劇降低;芒刺線尖端結球是電除塵器固有的現象,但因原料中配加煉鐵、煉鋼、熱電等生產環節的除塵灰(2007年萊鋼燒結廠消化除塵灰主要成分分析見表1),這些除塵灰為高鈣或高堿灰,導致除塵灰粘性強,結球肥大,把整個芒刺尖端全部包裹,造成電暈封閉,這也是造成除塵器運行效率降低的重要原因,對振打形式的改造勢在必行。
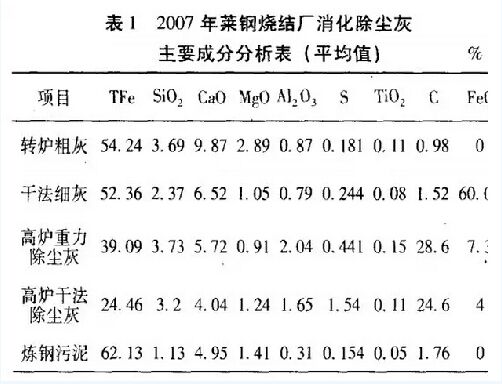
(5)對于二、三電場收集下來的輕質絮狀粉塵,氯化物含量較高,是造成除塵器清灰困難的主要原因,其含鐵較低,利用價值不大,返回料場重新利用會造成惡性循環,加劇了電場的負荷,因此將二、三電場除塵灰外排,不再進入燒結生產的閉路循環。 2兩臺105㎡燒結機機頭電除塵提效改造及新技術的綜合應用 充分考慮此工程為老廠區、老設備改造,作為萊鋼重點環保治理項目,幾經修改方案,最大程度地保留原有設備,縮短現場施工周期,使機頭除塵器性能實現最為合理、有效地提升。 新建249㎡電除塵器,單獨負責1#105㎡燒結機頭煙氣的凈化,249㎡電除塵器技術參數見表2.
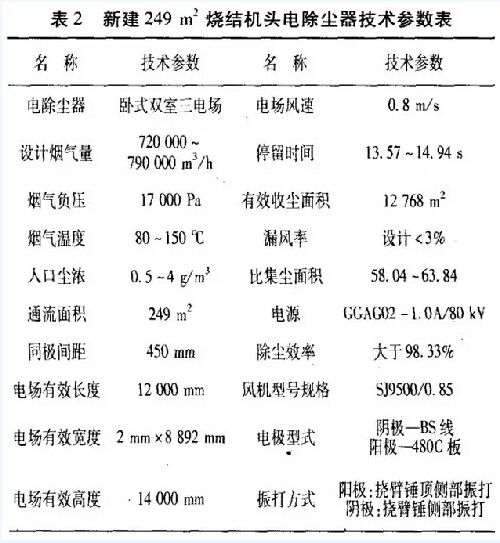
將原有1#、2#105㎡除塵器進行合并,改造250㎡電除塵,負責2#105㎡燒結機頭煙氣的凈化。 原125㎡電除塵器設計煙氣量570000m³/h,電場風速1.27m/s,燒結系統改造后,兩臺除塵器煙氣量為720000m³/h,單臺煙氣量360000m³/h,電場風速為0.8m/s,延長了煙氣停留時間,從工藝參數上滿足了機頭除塵器的除塵要求。原進氣煙道經沉降室(長*寬=12m*7m)后進入除塵器,改造后吸風管經30度彎頭進入鏈接異徑三通管,分別進入原125㎡電除塵器沉降室,在沉降室進氣端加電動閥門,調節閥門開度和增加導流板、阻流板等措施,保證兩臺125㎡電除塵器煙氣量的均勻性和壓力損失的平衡。 所有管道內用耐磨襯增加耐磨強度,新沉降室內部涂抹高溫耐磨襯,外部加保溫。 改造前后對比見圖1.
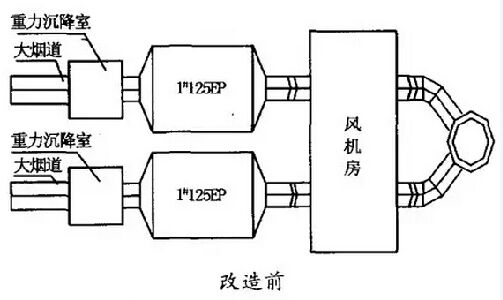
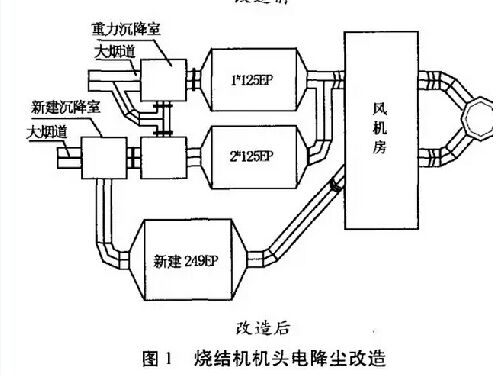
同時針對燒結機機頭粉塵的特點,為保證收塵效率,新建249㎡除塵器還采取了6項技術措施。 2.1芒刺線技術改造 原125㎡電除塵器極配型式為C型480mm極板配備RS芒刺線,新建除塵器改為C型480mm極板配備BS管狀芒刺線。陰極線采用BS管狀芒刺線的優點是:起暈電壓低,電暈電流大,電流密度均勻,有效消除電暈盲區,電風強,剛度大,使用壽命長,使粉塵充分荷電,吸附在陽極板上,提高收塵效率。 2.2芒刺表面涂覆特氟龍材料 特氟龍高性能特種涂料是以聚四氟乙烯為基本樹脂氟涂料,典型特征是不粘性、耐高溫和耐化學品腐蝕,三電場除塵灰主要含的是輕質絮狀粉塵氯化鉀及堿金屬再結晶物,其本身呈白色,比重特別輕,粘性大,浸潤性差,吸濕性強,受潮后易粘附在極線上不易清除。將第三電場芒刺線表面涂覆特氟龍材料后,大大降低了粉塵與極線之間的粘附力,有助于極板、極線的清灰,保證除塵設備設施的高效運行。 2.3陰極振打傳動防積灰技術 原125㎡電除塵器的陰極振打傳動密封防積灰方式為方形箱體結構加防塵板設計型式,這種方式箱體內容易積灰、受潮,致使振打磁軸表面產生爬電,造成電場短路。此次提效改造將瓷軸箱體下平面設計成斜面的樣式,無防塵板并定期進行自動或手工吹掃,保證瓷軸箱體內粉塵沿斜面流入電場內,有效防止箱體內積灰及磁軸爬電現象,保證長期高效供電。瓷軸箱體放于立柱外側,立柱內側按箱體下平面斜度作密封處理,提高除塵效率。 2.4二、三電場除塵灰外排的應用 萊鋼多種固體廢棄均返回到燒結配料之中,導致燒結機頭二、三電場的收集下來的粉塵,質輕、色白,主要成分是輕質絮狀粉塵氯化鉀、氯化鈉,二、三電場除塵灰含鐵量分別為14.87和9.85,其可利用價值不高,此次將每個電場的除塵灰各用一套輸灰系統分別收集,一電場除塵灰經集合刮板機回收利用,二、三電場除塵灰經集合刮板機,排至集合灰倉,加濕后外排。 2.5聲波清灰器在機頭除塵器的應用 經實踐證明,電除塵器安裝聲波清灰器后,各項運行參數明顯改善,效果明顯,特別二次電流升高較大,灰倉排灰順暢。本工程中在原1#、2#105㎡、新建249㎡除塵器的頂部、雙側部、各灰斗分別安裝了36臺、30臺,共計66臺聲波清灰器,保證電除塵器極板、極線的清灰效果及電場對粉塵的捕集效率,解決了灰斗內積灰架橋、板結。 2.6特殊密封材料的有效使用,減小設備漏風率 為降低漏風率,對灰斗、進出口法蘭連接處,采用特殊密封材料密封,人孔門采用雙層結構,硅橡膠材料密封,對陰陽極振打穿軸處采用密封填料壓蓋裝置;陽極振打傳動裝置與殼體連接處設有密封填料盒,并采用四氟板材料進行密封,從而減少轉動區域可能造成的漏風;進出口膨脹節連接處采用四氟帶進行密封,降低設備本體的漏風率。 3結論 通過對1#、2#105㎡燒結機頭除塵器提效改造,電除塵各項運行參數明顯改善,特別是二次電流升高較大,有效功率提高到74%以上,提升了電除塵的除塵性能,降低了粉塵排放濃度,排放總量大幅度削減,但粉塵排放仍然較高。如何進一步提高燒結機頭除塵器效率還有待于進一步研究。
|